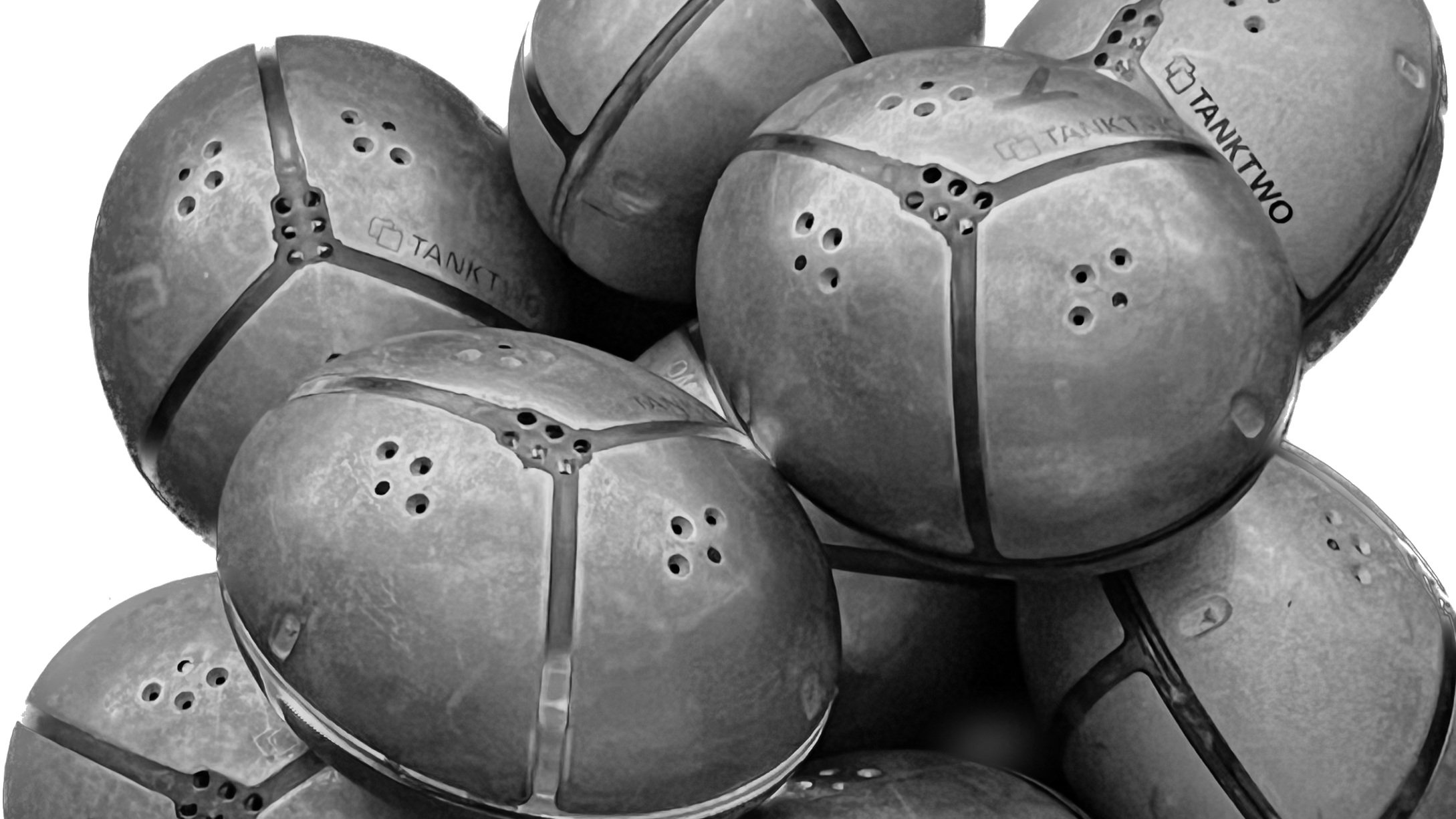
The smart little space egg that can
“How are your balls?” — that’s my mom asking me how my business is going.
The balls, of course, aren’t your typical spherical objects. The nerdy term is “ellipsoid” and they’re specifically designed so we can squeeze as many battery cells into a container as possible.
Those mighty little balls, called String Cells, have more than what meets the eye. They’re designed to overcome the limitations of today’s electric vehicles so commercial users no longer have to design their businesses around those restrictions — making electrification at scale an economically-feasible business case.
Let’s start from the beginning…
In 2009, I saw the potential of combining electrification, mobility, and data. I started to wonder why people keep saying electrification “wasn’t going to happen” in transportation.
Why?
Simply put, people can roll into a gas station, pump the gas in five minutes, and drive 300 miles. You can’t do that with electric cars.
Why?
Energy stored in traditional vehicles is in liquid form so all the infrastructure and business models are built to handle fuel as a liquid. Meanwhile, energy is stored in a monolithic “block” of battery in today’s electric vehicles and requires a completely different handling method that doesn’t fit into today’s consumer mindset or operating procedures of commercial fleets.
But.
What if… switching to an electric fleet doesn’t require companies to change their operational procedures or business models?
What if… we have a system that eliminates charging/idle time and range anxiety?
What if… we make batteries behave like a liquid so they can be handled like gasoline?
A liquid is just a bunch of tiny molecules that can organize themselves inside a container in the most compact and efficient way possible through “random packing.” What if we can make battery units behave the same way… with similar handling characteristics of liquid fuel, essentially behaving like a bunch of very big molecules?
To determine a shape that allows for the highest packing density, I talked to a friend who was an organic chemist and a professor at Yale University. Then, I turned to origami to explore random packing with flat surfaces (i.e., circuit boards) and the first battery prototypes looked like soccer balls (dodecahedrons, to be exact.) I also investigated a newly discovered carbon geometry (the Bucky Ball) and learned about the high lubricity factor of certain carbon compounds, which allows molecules to slide past each other with very low friction. It was obvious that the behavior of liquids was a material handling concept with legs.
Finally, I took the idea to Juha, a super-gifted mechanical engineer (now Tanktwo’s Lead Engineer.) It took him a few years (plus a ton of calculations) to conclude that the optimal packing density could be achieved by creating an ellipsoid with a specific semi-axis ratio (i.e., the ratio between width, length, and height.)
He even invented a highly-sophisticated software program to simulate the behaviors of ellipsoids so we could determine the optimal shape for achieving the highest packing density. Using complex physics engines, we predicted how the shapes interact with each other, with friction, and with gravity in the real world as they’re being “poured” (i.e., through bulk-handling) into a container.
And we determined the final shape for our batteries, which we called the String Cells.
The string cells aren’t just space-age cool. . .
The smart space eggs, despite their alien-like appearance, often use the most common lithium-ion battery chemistry (just like your smartphone!) because it’s the most cost-effective technology for a wide range of applications. However, we can use any battery chemistry as required by the application.
Instead of reinventing the battery chemistry, we make the batteries smart. Each cell has a unique identifier baked into a silicon chip. The chip, essentially a mini-computer, has the ability to protect the integrity of the cell and the system — meaning that a cell won’t put itself on fire even if it receives a command to do so. Also, it will shut down automatically when at risk of overheating to prevent a fire, even without central command.
The chip also measures relevant parameters — voltage, current, temperature, and optionally acceleration, even air pressure, pH, and more. The information can then be used to analyze performance, optimize usage, and maximize battery life.
Meanwhile, cells in a tank can communicate with the “outside world” through optical signals, radio frequency, or direct electrical contact. As such, a centralized system can be used to monitor the behavior of every cell no matter where they are so the user can optimize the performance of each battery unit in real time.
Last but not least, all the external contact points can switch between being positive or negative terminals at any time. As such, an electric circuit can be completed when cells are in a random packing environment to approximate the behaviors of “molecules” in liquid fuel.
. . . They also eliminate the biggest roadblocks to electrification
The ellipsoid form factor and the “smartness” allows for random packing, which makes bulk handling possible. From there, we can create a system that permits operational freedom.
When the string cells can be handled as a liquid fuel, existing business models, operations, and infrastructure can be used to support electrified commercial fleets with minimal adjustments
In addition, each cell acts independently. If one (low-cost) cell fails, you’d simply swap it out. A non-functioning cell won’t affect the performance of the pack. This is very different from traditional battery packs, in which one bad cell could cause a significant loss in power output or render the entire battery pack useless (as in the case of Nissan Leaf and Chevy Volt.)
The limitations of electrification, such as high capital outlay, range anxiety, low resell value, questionable durability, unpredictable cost of ownership, etc. are therefore eliminated. Instead of having to design business processes around the limitations of the tool, organizations can have the tool adapt to their operations.
Since the string cells are infinitely customizable, usage and resource allocation can be optimized for individual business cases by changing the batteries’ behaviors to maximize profits.
The nitty-gritty of this patented technology
The String Cell is one of the 7 patent families owned by Tanktwo, designed to position the company as the only global provider of a complex ecosystem bridging electrification, mobility, and data analytics. Here are some key areas covered by the String Cell patent family:
Each String Cell has interchangeable positive and negative voltage supply terminals and three or more contact pads on the outer surface to create a dynamically configurable connection unit that makes random packing — and therefore, bulk handling — possible.
The interchangeable polarity and multiple contact surfaces also allow an electric current to be drawn from a String Cell along different directions and different routes (e.g., via a low-resistance path). Users can also define a bypass route or create additional connections. This increases the dynamic reconfigurability and programming possibilities of each tank.
The contact areas can cover more than 60% of the outer surface of the housing. They can be maximized to ensure the highest probability of electrical contact of each cell with another String Cell or contact surfaces of the tank.
Each String Cell is equipped to measure the current flowing through any of its contact areas. This allows for real-time monitoring of the cells during operation.
The contact areas also allow for the sending and receiving of wireless programming or galvanic signals (e.g., electromagnetic, radio frequency signals, monochrome light, infrared, laser), typically from a tank control system, to adjust the behaviors of each String Cell based on usage and performance requirements.
Each String Cell has a memory unit with a unique identification code, making it possible to program each individual Cell to optimize the performance of the battery pack.
The ellipsoidal shape of the battery units results in high random fill ratios (typically over 70%) of nearly arbitrary shape and size, as well as good immobilization of String Cells in the container.
The String Cells are designed so they’re small enough for convenient bulk handling at a reasonable cost while large enough to store a significant amount of energy cost-efficiently. However, smaller or larger units of various shapes can be created for special applications.
The String Cells are programmable so they operate in suitable duty cycles to serve various needs. For example, 90% of the time may be reserved for power delivery and 10% of the time may be reserved for bidirectional communication with the tank control system.